ICC has process-cycle that is Material Development, Manufacturing Process, Evaluation / Analysis, and Engineering to create products by composites. And we resolve rapidly technical problems by supporting the technical fields from product design to manufacturing, and promote the use of composites.
Research
Technical fields
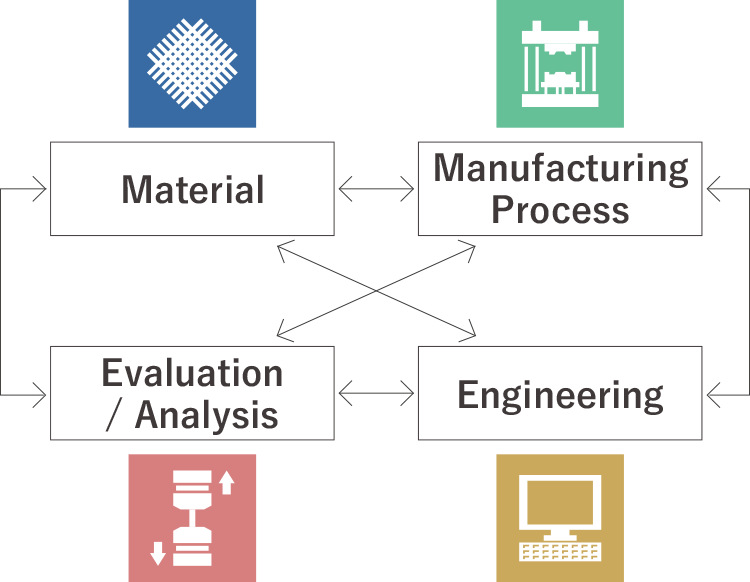
Material
-
Matrix resin
Intensively promoting R&D on Thermoplastic Epoxy Resin (TPEp) which has both thermoplastic and thermosetting characteristics. TPEp is superior in mechanical characteristics such as toughness, stiffness, bonding strength etc. Furthermore, it is applicable to various molding processes. ICC is also working on application research for composites whose matrix is in situ-polymerization thermoplastic resin like TPEp.
-
Preform
High-performance FRP uses various types of reinforcement, not just continuous fibers. ICC is working on laminates based on unidirectional tape and random sheets of chopped tape. For random sheets of chopped tape, our goal is to define its relationship between structural and mechanical properties and develop it as a designable material.
-
Interface
Interfacial adhesion between the fiber material and the matrix resin has a significant affect on the properties of the composite material. To improve it, our approach is surface treatment with plasma, compatibilizers, etc.
Evaluation/Analysis
-
Material characteristic evaluation
In each R&D phase from material to forming, ICC can perform appropriate composite tests based on JIS (Japanese Industrial Standards), ASTM and ISO standards etc. Such tests are effective in accelerating / reducing the R & D timescale.
-
Structure characteristic evaluation
Apart from material testing, structural scale evaluations such as sandwich structures and fitting structures are more important for FRP. ICC has a test facility that can cover medium size test pieces under high load.
-
NDE (Non- Destructive Evaluation)
Microscopic internal structure of FRP can be evaluated by microscope X-ray CT or 3D ultrasonic NDE (Non- Destructive Evaluation). These NDE technologies are used to clarify material / structure characterization. Recently, ICC is investigating the evaluation method for fiber alignment and resin void using new X-ray CT techniques such as phase imaging.
Molding Process
-
Double belt press
Using double belt press machine, we are developing manufacturing process of continuous thermoplastic laminate and machine system.
-
Press molding
Press molding is so important process, not only to form the shape but also to give the specified characteristics to the end product. Throughout heating-up/pressure/cooling-down process, ICC targets to set up the intelligent press molding system by using sensing, AI technologies in heating-up/pressure/cooling-down process.
-
Continuous molding
We are developing a high speed pultrusion process for rod manufacturing that can be widely used in infrastructure applications. In parallel, a continuous compression molding process / machine is also under development for the production of long, high strength parts.
-
RTM
Using HP-RTM equipment, we are studying mass production HP-RTM/C-RTM/wet molding process technologies of thermoset FRP. Also VaRTM process for big size/high quality parts manufacturing is under study.
Engineering
-
Forming simulation
FRP has a strong anisotropy whose deformation significantly affects on formability ,on mechanical property of the molded parts and on resin flow in molding process etc. We are working on forming simulation approach for press forming and bending of FRTP parts. In parallel, we are approaching to measure necessary engineering parameters in order to feed back to the simulation.
-
Resin flow simulation
In resin flow molding such as HP-RTM, the flow behavior of resin greatly affects the quality of molded parts. Therefore we are using resin flow simulation and apply to the development of optimized molding process and preform of fiber material. We also study on obtaining permeability value from experiments for use in the simulation.
-
Structural design /simulation
In structural design of FRP, it is necessary to consider material properties, molding method, joining method, fracture mechanism, etc. Therefore, by using structural simulation, the composite is designed under consideration of its fabrication.